Fillet Weld Layout Approaches: Optimizing Joint Efficiency and Aesthetics for Structural Stability
In the realm of architectural engineering and fabrication, the importance of fillet weld style strategies can not be overemphasized. By diligently taking into consideration variables such as weld account optimization, product option, joint prep work techniques, welding procedure effectiveness, and aesthetic enhancement approaches, fabricators and engineers can attain an unified equilibrium in between capability and look in their bonded structures.
Weld Profile Optimization


Attaining an ideal weld profile entails a careful factor to consider of elements such as material density, joint configuration, welding position, and desired welding rate. In addition, the option of ideal welding criteria, such as voltage, current, and travel rate, is fundamental in regulating the form and dimensions of the fillet weld. Making use of advanced welding methods, such as pulse welding or robotic welding, can even more refine the weld profile to meet certain style requirements and quality standards.
Essentially, weld account optimization is an essential facet of fillet weld style that directly influences the total performance and dependability of welded joints in structural applications.
Material Option Factors To Consider
When thinking about material option for fillet weld style, the compatibility of the base steels is a critical element influencing the structural integrity of the joint. It is important to choose materials that not just weld with each other efficiently but likewise possess comparable mechanical residential properties to guarantee the lots is evenly dispersed between the weld and the base metals. Welding materials with vastly various buildings can bring about concerns such as stress and anxiety focus, early joint failure, or splitting.
Furthermore, the setting in which the bonded framework will certainly operate should be taken into account when choosing materials. Factors like deterioration resistance, temperature changes, and direct exposure to chemicals can all affect the long life and efficiency of the weld joint. By selecting materials that are appropriate for the desired application and environment, official source the total durability and dependability of the bonded joint can be dramatically improved.
Consequently, extensive consideration of material compatibility and environmental variables is critical in ensuring the weld joint's strength, sturdiness, and overall structural stability.
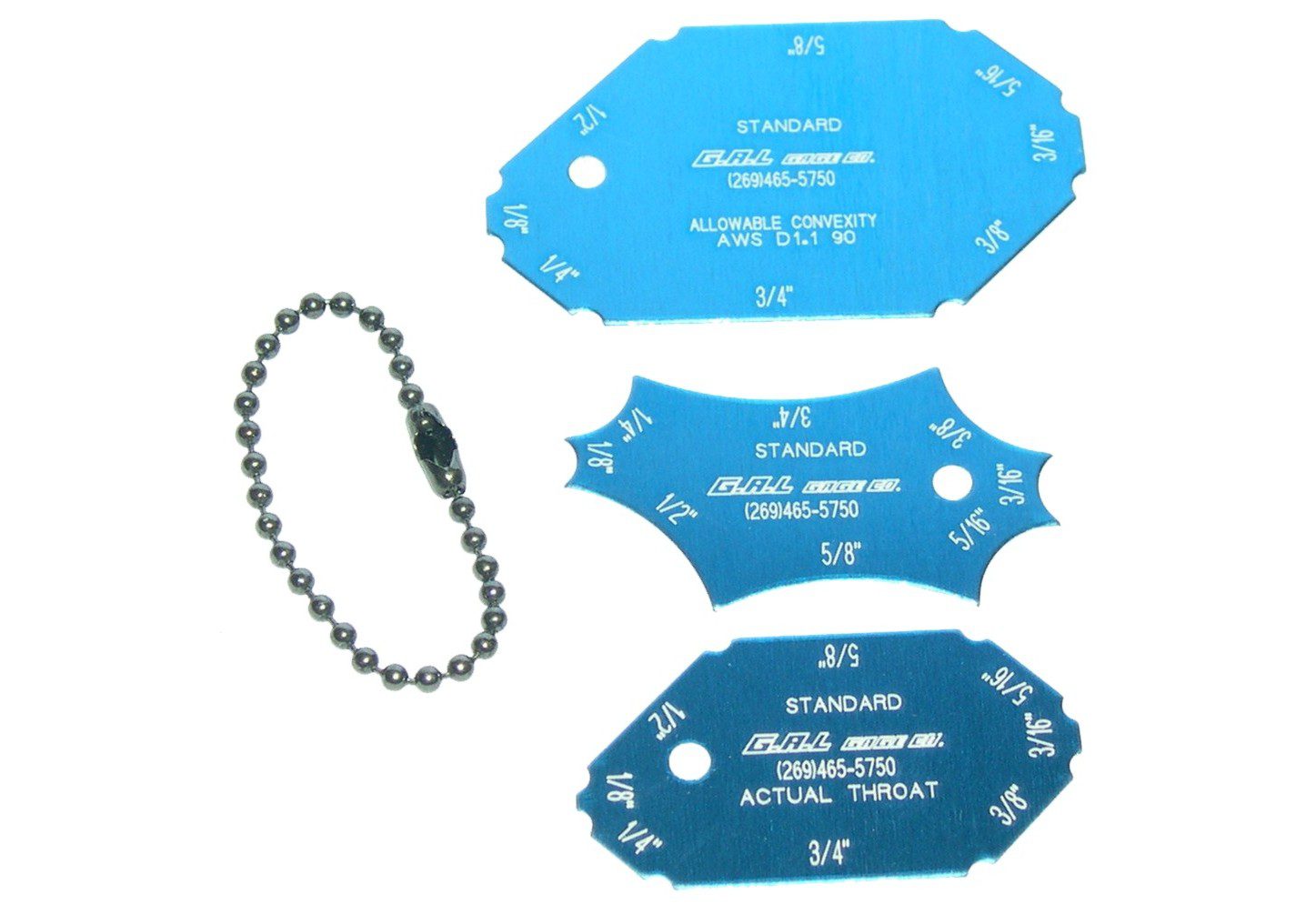
Joint Prep Work Techniques
Thinking about the essential role material choice plays in guaranteeing the structural stability of fillet weld joints, it is crucial to carry out accurate joint preparation strategies that enhance the connection in between the base steels. Joint prep work is a vital action that straight affects the high quality and strength of the weld.
In addition, tack welding the elements in location before the last weld helps maintain positioning and reduces distortion during the welding procedure. By thoroughly following these joint prep work techniques, welders can improve the total efficiency and looks of fillet weld joints while making sure structural sturdiness.
Welding Process Efficiency
Efficient welding processes are vital for attaining optimum performance and top quality in fillet weld construction. One key aspect of improving welding process performance is selecting the proper welding method. Elements such as product kind, joint layout, and welding setting have to be thoroughly thought about to figure out the most suitable method. As an example, processes like gas metal arc welding (GMAW) and flux-cored arc welding (FCAW) are frequently utilized for fillet welds because of their flexibility and speed (Gauge Fillet Weld).
Regular calibration of welding machines, assessment of consumables, and maintenance of welding lanterns can prevent downtime and rework, ultimately conserving time and resources. Well-trained welders are a lot Go Here more proficient at readjusting parameters, fixing problems, and keeping consistent weld high quality.
Aesthetic Improvement Techniques
To maximize the high quality of fillet weld manufacture, applying visual enhancement techniques can play a vital role in making sure precision and precision throughout the welding process. Visual aids such as weld dimension gauges and multiplying lenses can help in evaluating weld accounts and dimensions properly. By integrating these aesthetic improvement More about the author techniques right into the welding procedure, welders can attain not just structurally audio fillet welds yet additionally visually enticing results that fulfill sector standards.
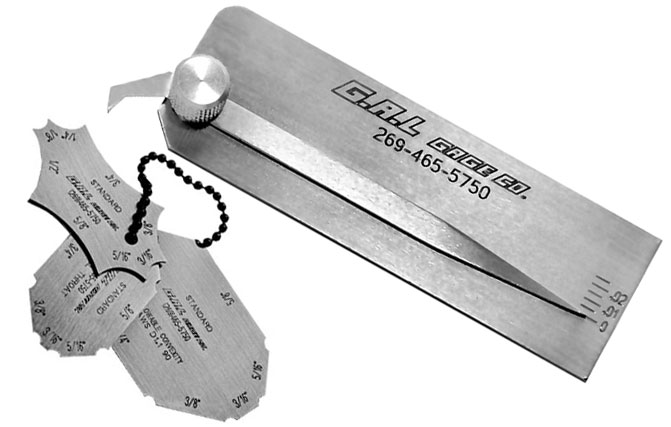
Verdict
To conclude, maximizing fillet weld style entails cautious consideration of weld profile, material option, joint preparation, welding procedure efficiency, and visual enhancement methods. By carrying out these approaches, architectural integrity can be improved while likewise achieving aesthetic appeal. It is essential to prioritize both efficiency and visual appeals in fillet weld style to guarantee the overall quality and toughness of the joint.
By thoroughly taking into consideration aspects such as weld account optimization, product selection, joint preparation techniques, welding procedure performance, and aesthetic improvement engineers, methods and producers can attain an unified equilibrium in between functionality and look in their welded structures.In the realm of fillet weld layout, maximizing the weld profile plays an essential role in making sure structural honesty and efficiency. The weld account, which consists of the size and shape of the weld cross-section, straight influences the circulation of stress and anxiety and load-bearing capability within the joint. It is necessary to select materials that not just bonded together successfully yet likewise have comparable mechanical residential properties to make certain the load is equally dispersed in between the weld and the base steels - Gauge Fillet Weld.In verdict, optimizing fillet weld style entails mindful factor to consider of weld profile, product choice, joint prep work, welding process effectiveness, and visual improvement techniques